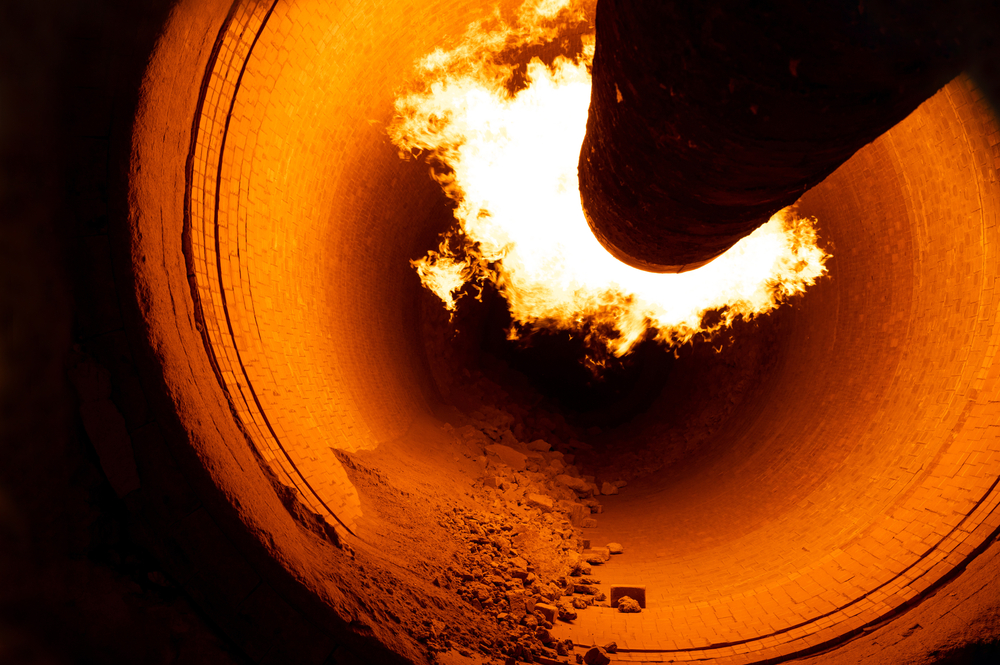
“Aside from water, there’s no material on Earth we use more than concrete,” tweeted Bill Gates in May. “That’s why it’s so important to figure out how to decarbonise it.” Indeed, houses, skyscrapers, dams, bridges – all types of buildings and infrastructure – rely on concrete for its strength, durability, flexibility and affordability. It’s no wonder then that global demand for cement, which hardens into concrete when mixed with water and minerals, is forecast to rise by 48% to 6.2 billion tonnes by 2050 – and that decarbonising cement is an inescapable part of the climate agenda.
In the recent mass urbanisation of China, the country used more concrete between 2011 and 2013 than the US did in the entire 20th century. Even though Chinese concrete use is now slowing, consumption in India, Africa and other Global South nations is set to explode alongside their population growth and economic development. This, however, poses a problem for the environment: concrete is responsible for 8% of global carbon emissions, or more than three times the emissions produced by aviation, and there is no easy way to get rid of them.
According to the Intergovernmental Panel on Climate Change (IPCC), the world needs to reach net-zero greenhouse gas emissions by 2050 for a good chance of keeping global warming to a relatively benign 1.5°C. However, due to the cement industry’s long-lasting assets, 2050 is just one investment cycle away. That means that this decade all major new investments need to be net-zero compliant and decarbonising cement technologies need to be deployed on a large enough scale to trigger significant cost and emission reductions in the following decades.
“If it was so easy, it would have been done by now,” says Radhika Lalit, principal for a cement and concrete initiative at the think tank RMI. “There is no one single silver bullet to decarbonise this sector; that is why it is traditionally known as one of the hard-to-abate sectors.”
Decarbonising cement faces four main challenges. First, 53% of the sector’s emissions are “process emissions” that come from the process of producing clinker, a strengthening material that is the backbone of cement as we know it: limestone and clay generate CO₂ as they are heated together in a rotary kiln. Second, another 35% of the sector’s CO₂ derives from burning fossil fuels to reach the 1,500°C required for the chemical reactions (calcination) inside that kiln. Third, there is the projected growth in demand for cement, driven primarily from developing markets such as India. Finally, there is the simple fact that it has always been a highly localised market, so decarbonising cement relies on compliance from a bewildering array of regional stakeholders, all with varying circumstances and priorities.
Decarbonising cement with less clinker
In the absence of a silver bullet, the approaches and technologies aimed at decarbonising cement are manifold. One of the simplest options is to just use less concrete. Typically engineers veer on the safe side for strength – for obvious reasons – when designing buildings and infrastructure, but research from the Global Cement and Concrete Association has shown that using concrete more efficiently could result in 20% lower emissions from buildings.

US Tariffs are shifting - will you react or anticipate?
Don’t let policy changes catch you off guard. Stay proactive with real-time data and expert analysis.
By GlobalDataThat is if the building needs concrete at all. An alternative solution is to substitute the concrete for a less emissions-intensive structural material such as sustainable timber. “Using engineered timber instead of concrete can reduce the embodied carbon emissions of a building over its whole life cycle by up to 60%, though some estimates are much lower, depending on the study,” says Dr Peter Schniering, CEO of the climate innovation think tank Future Cleantech Architects. “Of course, this relies on the availability of a sustainable supply of wood.”
You can also use less clinker in the concrete itself. In its place, a producer can use what are called supplementary cementitious materials (SCMs) such as fly ashes, slag cement (ground, granulated blast-furnace slag) and silica fume. “It depends on the material you use and the specific blend, but you can replace up to 50% of clinker with these SCMs,” says Schniering. Some low-carbon cement manufacturers believe they can reduce the proportion of clinker in cement even further, to as low as 20% in the case of Ecocem.
Indeed, a new Alliance for Low-Carbon Cement & Concrete launched on 30 May in Brussels aims to deliver a zero-carbon cement and concrete value chain by 2040. Supported by Bill Gates’s Breakthrough Energy, an inaugural study modelled a decreasing clinker-to-cement ratio in Europe from 78% in 2020 to 60%, 50% or 40% by 2050, which could cut the sector’s annual CO₂ footprint by 28%, 40% or 52%, respectively, the research suggested. The EU’s clinker-to-cement ratio “is traditionally much higher than in the rest of the world”, the Alliance noted.
There are also exciting innovations that offer new options for decarbonising cement: alternative concretes made from raw clays promise up to a 50% reduction in CO₂ emissions. Another route is replacing limestone as a feedstock to produce ordinary portland cement with alternative raw materials such as calcium-silicate rocks, which do not have CO₂ embedded in them. There is also a promising new alternative clinker based on magnesium oxides derived from magnesium silicates that is in its early stages of development. The latter two could potentially be carbon negative as the magnesium found in these rocks naturally sequesters CO₂.
Then there are other approaches that chemically enhance the strength of the concrete, meaning you can afford to use less of it. For instance, one such technology is called carbon curing, which involves injecting CO₂ into precast concrete, thereby reducing its emissions by up to 50%.
Carbon capture and storage remains the backstop
However, the decarbonising approach that remains most popular among the world’s leading cement producers is using carbon capture and storage (CCS) technology to capture the emissions from the legacy cement production process. Although there are no commercial-scale CCS projects in action yet, there are prototypes in development across the world. However, Schniering warns there is a big difference between what is being communicated by governments and producers and the reality on the ground. “If you talk to communities where there is a lot of cement plants, they have no clue how to manage the massive capex that would be needed to build up CCS facilities,” he says. It truly is a massive investment to retrofit a cement plant with carbon capture. “We are talking in the order of billions of dollars and so it is very, very cost intensive,” says Ben Skinner, a senior associate on the cement and concrete team at RMI.
From a technical perspective, there are a variety of approaches to CCS. The most common is the use of oxyfuels, which capture the carbon by adding oxygen to the process. Alternative approaches include direct-separation and post-combustion, which have their own different advantages and drawbacks. “The oxyfuel pathway has the highest potential of capturing and storing emissions, but it is not very mature yet,” says Schniering. There are challenges to the CCS process. For instance, the conventional process of calcination does not produce a pure – easily capturable – stream of CO₂; instead it is mixed with other gases created by the fossil fuels.
This brings in another approach to decarbonising cement: replacing the burning of fossil fuels in the cement production process with electrical heat – the advantage being a pure stream of CO₂ coming from the limestone during calcination. “But when we talk to cement producers, they tell us this is not an easy thing to do,” caveats Schniering.
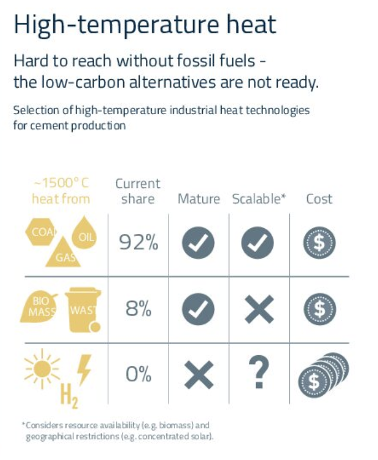
Why? You need very high temperatures to produce clinker. First, you need to reach about 900°C to produce calcium oxide. After that you need 1,500°C to create the clinker itself. You can electrify part of the process, but you still need conventional fossil fuels to reach 1,500°C. You could replace that process with a different technology such as electrolysis, which changes the chemistry and means you do not need such high temperatures, but incorporating it into a traditional plant increases capital and operating costs.
“It is very, very complex,” admits Ingrid El Helou, a cleantech analyst at Future Cleantech Architects. “But electrification has to be coupled with CCS, because you still have the emissions that are coming from the breakdown of the limestone.
“A lot of these electrification options are still in their infancy,” she adds.
What is taking so long?
So, the solutions are there – if, granted, they all come with their difficulties. However, in truth, there are more structural reasons behind the slow take-up of decarbonising cement solutions by producers.
Chief among those reasons is that cement is a very traditional and incumbent industry. Companies across the world have been producing portland cement for more than a century and are typically very conservative. “The process has been optimised for decades on its efficiency and cost competitiveness, but not on its carbon intensity,” says Schniering.
In the same vein, strict safety regulations on the industry have accumulated over the years, often as a response to catastrophes such as the collapse of a bridge in Genoa, Italy, in 2018, which left 43 dead. However, those regulations and building standards can make it hard to optimise construction from an emissions perspective. “Sometimes it’s impossible, because of the regulation, for a new type of alternative cement not built on limestone to enter into the market because it has to go through all these verification and certification procedures,” says Schniering. “So, that needs to be sped up and made more flexible, by focusing on performance-based standards rather than prescriptive content-based standards.”
Cement is also a very localised market. As limestone is so abundant, countries are quite independent when it comes to manufacturing cement. To ensure countries maintain this autonomy when making the switch to alternative cements or concretes, abundancy of the raw materials is crucial, according to El Helou. “The amount of influence you have to change things isn’t on a very global basis – you have to be very specific and have solutions at the regional level, which makes the process more complicated,” adds RMI’s Lalit.
Finally, there is our insatiable appetite for cement; there is little incentive for the cement industry to change if we keep buying cement in the quantities that we do. The implications of creating a high embodied carbon project are not detrimental enough to reshape business as usual. “This is changing though, with embodied carbon targets in place for planning permission in places like London, for example, and targets being set by [construction] clients,” says Natasha Watson, embodied carbon lead at UK engineering consultancy Buro Happold. “But with less than seven years until 2030, it may not be fast enough.”
Getting cement to net zero
So, what needs to be done to decarbonise cement and get the industry on track for net zero by 2050? A good place to start would be with the key tenet of carbon reduction: use less stuff. Engineers and designers are familiar with creating efficient solutions; however, they need to think more about what “less” means, according to Watson. “Do we need another speculative office? New high-end housing? To raze an existing high street to rebuild a new shopping centre?” she asks. “We should ask whether a building is needed at all or if an existing building can be retrofitted to suit.”
Governments, the leading buyers of cement, also have powerful agency to force change in the industry through green public procurement. Even though green cement is more expensive than the traditional variety, the overall added cost to an infrastructure project is relatively low. A World Economic Forum study found that although the premium for green cement is more than 50%, it would raise the end-cost for consumers by less than 5%. Similarly, the Mission Possible Partnership, an alliance of climate organisations aiming to decarbonise the world’s highest-emitting industries by 2030, found that the extra cost to the consumer of using green cement to build a $500,000 house would be just 3%. “Governments can do a lot by opting for green cement and alternatives in public procurement – they have strong power to affect change via market pull,” says El Helou.
There is an obvious need for more support for research and development into new innovations such as alternative raw materials and binders, but policymakers also need to think about how they promote this kind of innovation. Lalit believes they should look to create more performance-based standards. “When you ask for proof of performance, then you could get different kinds of solutions rather than one standard one like adding this much SCM, this much slag, this much limestone – if you prescribe that, then it becomes very difficult for any innovator say, ‘well, I have something that is better’.”
“Alliance members all face the same challenge – standards are blocking the entry onto the market of their low-carbon product offerings,” said Justin Wilkes, executive director of the Environmental Coalition on Standards, a Brussels-based NGO and member of the new Alliance for Low-Carbon Cement & Concrete, at its launch. A European Commission official told the event that it wants to change these standards.
“We will develop a standardisation request for cement,” said Katharina Knapton-Vierlich, head of unit for construction at the Commission’s industry directorate. “[Standards] will be performance-based and technology neutral.” The Commission aims to unveil its request in the second half of 2024.

But the industry’s main ask of policymakers is for help with CCS. That could be through increasing access to CO₂ storage sites, developing CO₂ transport infrastructure or just supporting ongoing investment in the sector. “Also, we believe that carbon capture and utilisation (CCU) should be fully recognised through an appropriate regulatory framework,” adds Koen Coppenholle, CEO at CEMBUREAU, the European Cement Association.
CEMBUREAU is pushing the EU to unlock funding and simplify bureaucracy for CCUS projects, “because, in the first 10–15 years, EU help is needed to bridge the real cost of projects,” says Coppenholle. Specifically, decarbonising cement proposals from the industry include advancing a specific cement industry innovation funding round, wide-scale adoption of carbon contracts for difference for CCUS, allowing carbon use projects to run at least until 2050, and simplifying state aid rules. The organisation is also pushing for shorter permitting for decarbonisation projects, “as permitting is becoming a major bottleneck for our projects”, says Coppenholle. The EU is currently consulting on a new CCS strategy due for publication this autumn.
“The industry needs support here,” agrees Schniering. “Put yourself in the shoes of these traditional industry players, with all of these jobs and all of these established processes, and suddenly it all has to change so drastically. No wonder they want to opt for CCS – it is very much in line with the existing process.”
“In truth, what is needed is a technology-open public perspective on this and funding for projects in a comprehensive strategy with various pathways including demand reduction, energy efficiency measures, CCS, as well as completely new types of technologies,” Schniering concludes.