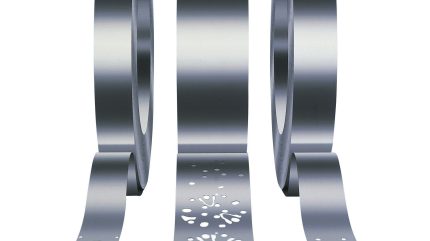
The global demand for heating and cooling is surging in response to climate change and rising living standards, especially in urbanised areas. However, the spotlight is turning towards the environmental cost of air conditioning and heat pump systems, with buildings accounting for approximately 28% of global CO₂ emissions. The race is on to refine the technologies that regulate indoor climates without compromising the planet.
The essential role of compressor valves
Air conditioning systems are increasingly designed to offer year-round functionality, incorporating both cooling and heating technology. While this dual capability addresses comfort and energy efficiency, it also demonstrates the urgent need to reduce emissions linked to HVAC operations given their increased usage. A critical, though often overlooked, component in achieving these reductions lies deep within the systems themselves: the compressor valve.
This small component plays a pivotal role in the energy dynamics of an HVAC unit, and its performance and durability are directly tied to the materials from which it is made. With compressor valves operating under intense pressure and temperature variations, the challenge has long been to engineer materials that can withstand such conditions without degrading performance or contributing to inefficiency.
Enter Freeflex® – a new range of next-generation stainless steel alloys developed by Swedish materials technology company Alleima. The two Freeflex® alloys build on a heritage of high-performance steels and have unique compositions that set them apart, highlighted by elevated levels of carbon, chromium and copper, which translates into superior mechanical strength and resilience under fatigue. According to Remco Jongen, global product manager at Alleima: “The two Freeflex® alloys offer superior fatigue and wear resistance, allowing for more aggressive valve designs that contribute to improved energy efficiency in compressor operation.”
The next generation of sustainable compressor steel
It is difficult to assign a fixed percentage to the contribution of Freeflex® to energy savings, as performance ultimately depends on the design of the compressor, but it is telling that Freeflex® Core, one of two advanced alloys in the Freeflex® product line validating the role of the Freeflex® family, has already been adopted as a valve material in several new high-efficiency compressor models now in serial production. These commercial rollouts offer clear, market-led validation of the role of Freeflex® in enhancing the energy performance of compressors, particularly in high-demand applications. While its predecessor, Hiflex™, remains a high-performance solution in its own right, the material properties of Freeflex® elevate it to a level better suited for the next generation of compressor efficiency requirements.
One of the key advantages of the enhanced material properties of Freeflex® is that it enables a reduction in the thickness of the compressor valve due its superior fatigue and wear resistance allowing the valve to endure millions of pressure cycles despite being thinner. Additionally, the optimised microstructure of Freeflex® provides greater stability and dimensional control, which is crucial for manufacturing thinner components with precision. These attributes combine to improve energy efficiency, as thinner valves respond more quickly and require less force to operate, while also helping to reduce noise through decreased mechanical resistance and vibration.
Beyond efficiency, Freeflex® also supports improved acoustic performance. Quieter operation is becoming a hallmark of next-generation heat pumps and AC units, particularly as systems are miniaturised and installed in residential or noise-sensitive commercial environments. Though compressor noise levels are largely dictated by overall system design and operating conditions, the enhanced elasticity and structural integrity of Freeflex® allow engineers to explore configurations that reduce mechanical vibrations and operational noise compared to traditional martensitic steels.
Furthermore, around the world, regulatory pressure is mounting for HVAC systems to meet stricter environmental criteria. For example, the European Union and North America are phasing in tighter eco-design regulations to push compressor manufacturers to meet targets not only in energy efficiency, but also in compressor miniaturisation, refrigerant compliance and reductions in carbon footprint. While there are currently no specific material certifications for compressor valve steels, materials such as Freeflex® are designed to support compliance with these broader regulatory trajectories, acting as enablers for the future-proofing of HVAC products.
However, these innovations are not developed in isolation, and Alleima maintains close R&D partnerships with a range of compressor and valve manufacturers globally. These collaborations are critical to ensuring the two Freeflex® alloys are finely tuned for evolving compressor designs and allow for shared knowledge and iterative improvements to ensure that material advancements translate into tangible, system-level gains in the field. This convergence of material science, engineering design, and regulatory direction is reshaping the HVAC sector, with heating and cooling technologies becoming more integrated, especially in regions where heat pumps are displacing fossil-fuel-based heating.
According to the International Energy Agency, global demand for air conditioning is set to triple by 2050, so solutions that combine long-term durability with measurable energy savings will be essential to meeting that demand responsibly. Advanced materials, like the Freeflex® product line, are enabling a transformation in how heating and cooling systems are engineered, enabling the development of units that are cleaner, quieter and more efficient than ever before.
To find out more about Alleima’s compressor valve steels, including Freeflex® Core and Freeflex® Versa, download the whitepaper below.